- HOME
- Digital Transformation
- The 10 essential features of field service management software
The 10 essential features of field service management software
- Last Updated: October 8, 2024
- 112 Views
- 8 Min Read
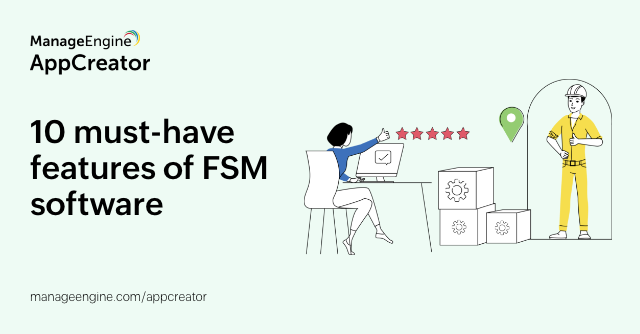
Ever had to juggle too many things during field service appointments? Scheduling appointments, tracking field teams, rechecking the work, and trying to piece it all together afterward—it's exhausting, right? That’s why you need field service management (FSM) software to handle the chaos. Think of FSM solutions as a helping hand that keeps everything in sync, making sure all the field operations run smoothly behind the scenes. So let’s start with the basics: what exactly is FSM, and why does it matter?
Field service management is all about managing teams that work outside the office. This team includes technicians, contractors, and maintenance staff. Essentially, it's the system that keeps your operations in check. It covers everything like job scheduling, dispatching, tracking, reporting, and even invoicing. With FSM software, businesses can simplify the chaos and make sure field teams stay connected and efficient—no matter where they are!
Why do you need FSM software?
Imagine managing your field service jobs through phone calls, emails, and manual logs. It’s a long, drawn-out, error-prone, and chaotic process.
FSM software takes all of that mess and organizes it into one easy-to-use platform. It keeps everything—from job scheduling to customer updates—in one place. You can streamline your processes and keep better track of what’s happening in the field. This ultimately makes your business more efficient and productive.
Now, let’s break down the top 10 essential features to prove why FSM software is important. To make this relatable, let’s imagine a day in the life of a field technician working at a food processing plant. To add extra flavor, let us assume each step is a scene. We’ll see, in turn, how each feature helps make the job faster, smoother, and more efficient.
Top 10 features of field service management software you should know about
Now let us delve into the food processing technician's day in a field service scenario.
Scenario: Prepping for the day
We'll come across some technical terms as we are getting into details.
Starting the day, the technician receives a notification saying the system has flagged a possible issue with the SVE 2520 AR—a vertical form-fill-seal machine used in the plant for packaging sauces into sealed pouches.
Before anything can go wrong, it is important to give our technician a heads-up to avoid any messy situations (literally, in this case—no one wants sauce everywhere).
The system also sends a warning that the sensor responsible for measuring the pouch alignment is malfunctioning. This malfunctioning could lead to misalignments, resulting in incorrectly sealed pouches that can spill the sauce. The alert gives the technician a heads-up to bring a replacement sensor.
1. Inventory management
Inventory management keeps track of parts, tools, and supplies in real time. This ensures that the technicians always have the right parts on hand, and that stock levels are automatically updated as parts are used or ordered.
Scenario: Stocking up
Before heading out, the technician checks the inventory levels using the FSM application, which shows what spare parts are available at the office. The system suggests bringing a replacement alignment sensor for the packaging machine and other small parts, like sealing gaskets (just in case), for the machine.
The technician reviews the inventory and ensures that the exact model of the sensor is in stock at the office. Thanks to inventory management, there’s no last-minute scramble, like searching for a sock in the laundry.
The system also flags that there’s only one replacement sensor left in stock, so the technician can request the relevant authorities in the firm to restock shortly. Then, the technician confidently packs the sensor and heads out, knowing everything needed is on hand.
2. Dynamic route optimization
Dynamic route optimization ensures that the technicians take an efficient route to their jobs. The FSM software uses real-time traffic data to provide the fastest and most fuel-efficient route. This feature saves both time and cost.
Scenario: The journey begins
Once the technician is ready to go, dynamic route optimization kicks in. The FSM software calculates the best route to the plant, taking into account traffic, construction zones, and the shortest path. This ensures the technician arrives as quickly as possible, minimizing delays.
While en route, if there's a traffic jam, the FSM system suggests a new route. The technician follows the updated directions, saving 10 minutes that would have otherwise been spent in traffic.
No stress, no honking horns, just smooth sailing!
3. Real-time communication and technician tracking
FSM software provides real-time communication tools to connect field teams with the office and customers. This allows for instant updates, coordination, and collaboration.
Scenario: Arrival check-in
Upon arriving at the plant, the technician taps “Arrived” on the FSM mobile app. The real-time communication feature instantly sends an update to the office, letting dispatchers and the back office know the technician is on-site and ready to begin repairs.
No more wondering, “Did they make it?”—everyone knows where the technician is. It is like when you check on your food delivery, except here it’s machinery being saved, not your dinner.
Scenario: Keeping tabs
During the repair, the technician tracking feature logs every action, from arrival to completion. The back office can monitor progress and update schedules accordingly.
While the technician works on the sauce sealing machine, the system logs each task—including the sensor replacement and motor check—updating the back office in real-time so they can adjust the day’s schedule as needed.
4. Multi-language support for global teams
Multi-language support ensures that technicians and teams operating in different regions can access the FSM system in their preferred language. This feature is especially helpful in global operations—it's like having a universal translator in your back pocket.
Scenario: Bridging the language gap
At the plant, the production team speaks primarily Spanish, while the technician is more comfortable with English. No problem—the FSM software offers multi-language support.
The technician uses this feature to review the service request in English. And, the production team sees the same request details in Spanish. Both sides understand the same information, allowing for smoother communication about the issue.
5. Custom workflow automation
Custom workflow automation allows businesses to create step-by-step processes tailored to their specific needs. It automates tasks like scheduling, parts ordering, and even generating invoices, ensuring that everything happens in a smooth, consistent flow.
It’s like following a recipe, but instead of cookies, you’re making machinery work perfectly again.
Scenario: Automated guidance
With custom workflow automation, the FSM software guides the technician through each step of the repair process. After powering down the machine, the software pulls up the exact procedure for replacing the sensor and recalibrating the system. It also suggests running a quick check on the conveyor motor, which was flagged during diagnostics.
The technician follows the automated workflow step by step: shutting down the machine, safely removing the faulty sensor, installing the new one, and then recalibrating the alignment system.
The workflow also reminds the technician to lubricate the motor and run a quick diagnostic test before finishing.
6. Field technician wellness monitoring
This feature monitors a technician’s workload, fatigue levels, and breaks, ensuring that they stay healthy and productive throughout the day.
Even machines need downtime—why not humans too?
Scenario: Avoiding burnout
As the technician works, the FSM system monitors the time spent on the repair and suggests a break if needed. Field technician wellness monitoring—the schedule workflow that has already been created—ensures that the technician don’t overwork, helping prevent burnout and keeping them alert during complex repairs.
After working on the repair for two hours straight, the software prompts the technician to take a short 10-minute break to avoid fatigue. This helps ensure the technician stays focused and alert for the rest of the job.
7. Reporting and analytics
With reporting and analytics, a FSM solution provides valuable insights into job completion times, customer satisfaction, inventory use, and much more. It helps businesses identify areas for improvement and optimize operations.
Scenario: Performance insights
Once the repair is complete, the technician uses the FSM software to generate a detailed report with the reporting and analytics tools. The report includes the time spent on-site, parts used, and diagnostics data from before and after the repair.
The report shows that the alignment sensor was replaced, the conveyor motor was inspected, and the machine was recalibrated. The FSM software also generates performance data, showing the improvement in machine uptime following the repair.
8. Financial management
Financial management tools in FSM software ensures accurate and timely invoicing, as well as tracking expenses and revenue for each job.
Scenario: Accurate billing, hassle-free!
Once the repair is logged, the FSM system uses the financial management features to generate an invoice for the client. It calculates the cost of the new sensor, the labor hours, and any additional materials used during the repair, ensuring the client gets an accurate and timely bill.
The technician enters the parts used, along with the labor time. The system automatically generates an invoice for $1,200, which is sent directly to the plant’s accounting team.
9. Customer relationship management
Customer relationship management (CRM) features in FSM software provide technicians with access to detailed customer histories, helping them deliver personalized and effective service.
Scenario: Personalized customer care
With CRM integration, the technician pulls up the full service history of the machine, including any past issues and repairs. This allows for a personalized approach, ensuring the plant gets the best service possible.
The CRM shows that this specific machine had a similar sensor issue six months ago. The technician can now investigate whether this is a recurring problem and offer a more permanent solution if needed.
10. Business apps integrations
FSM software integrates with other essential business tools, such as accounting, CRM, or ERP systems. This ensures that all data flows seamlessly across platforms without the need for manual entry.
Scenario: Seamless system sync
Finally, the FSM system integrates seamlessly with other business apps like the company’s accounting software, making sure all data syncs across platforms. This ensures that everything from invoicing to service records is automatically updated and available for future reference.
The job details, including the parts used and time spent, are automatically synced with the company’s accounting system, ensuring accurate financial records and smooth billing.
Ready to step up your field game?
Field service management isn’t just about sending out a technician and calling it a day anymore. It’s about tapping into some seriously smart tools to boost efficiency, keep your customers smiling, and make your whole operation run smoother. The right FSM software doesn’t just make your technicians look like heroes; it reshapes how your business handles everything—from scheduling and dispatching to keeping things maintained and communicating in real time.
Now, what if you could customize these elements to fit your business perfectly? That’s where ManageEngine AppCreator enters the scene.
ManageEngine AppCreator is a low-code platform that lets you build and customize solutions for field service requirements—no programming skills required.
Want to add specific workflows? Check.
Need it to integrate with your existing systems? You got it.
Want to make your mobile app feature-rich? Easy.
AppCreator gives you the flexibility to tailor custom solutions for your FSM requirements, just the way you need them.
Time to take charge of your field service operations with AppCreator
Why settle for rigid FSM software when you can create something that is tailor-made? With AppCreator, you get all the necessary features you need to develop robust FSM applications. You also get the freedom to tweak things so they work for you—no fuss, no coding headaches.
So, if you’re looking to help your technicians be more efficient, cut down on those annoying operational hiccups, and make your customers happier, it’s time to see what ManageEngine AppCreator can do for you.
Give it a go today and see how a personalized approach to FSM software can take your business to the next level—no magic wands required, just smarter tools!